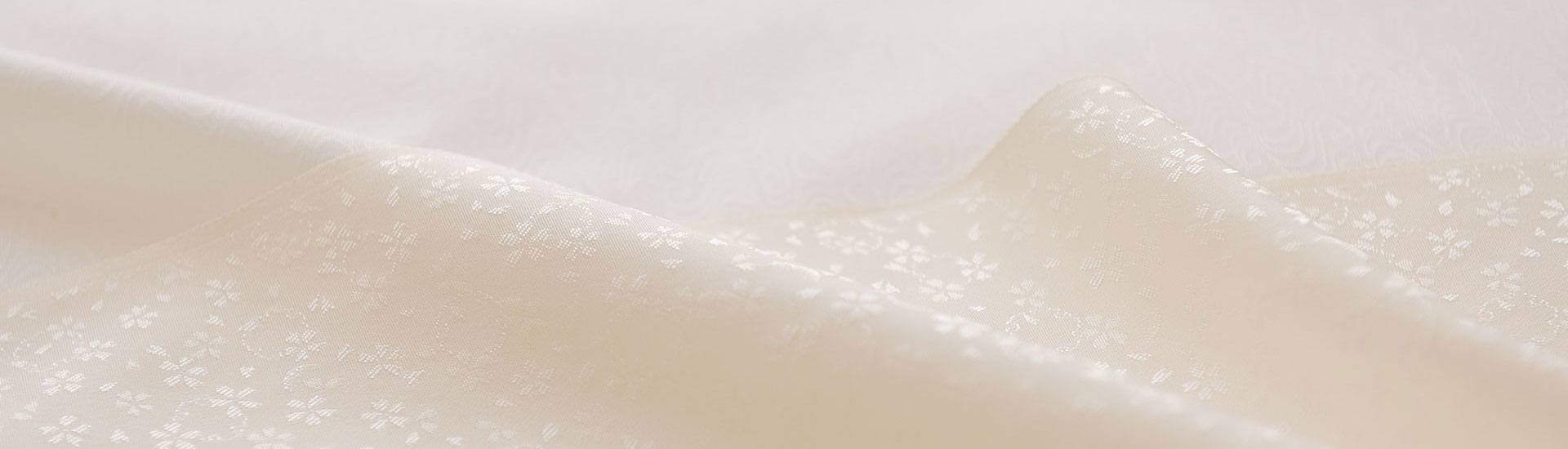
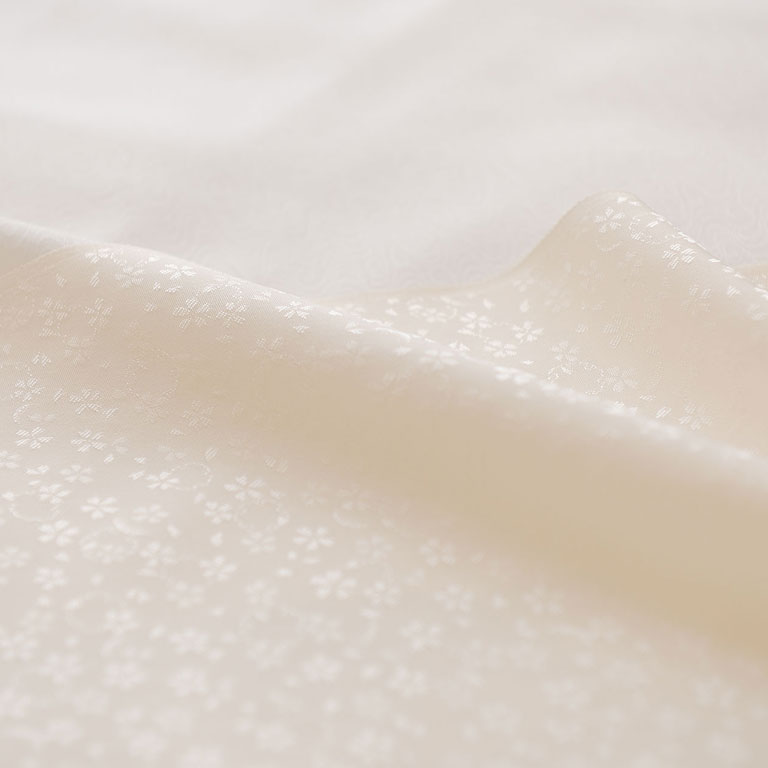
Creating Kimono Completely In-House
This was a new challenge, which, building on our ever growing ingenuity,
called for improvements in technique and quality.
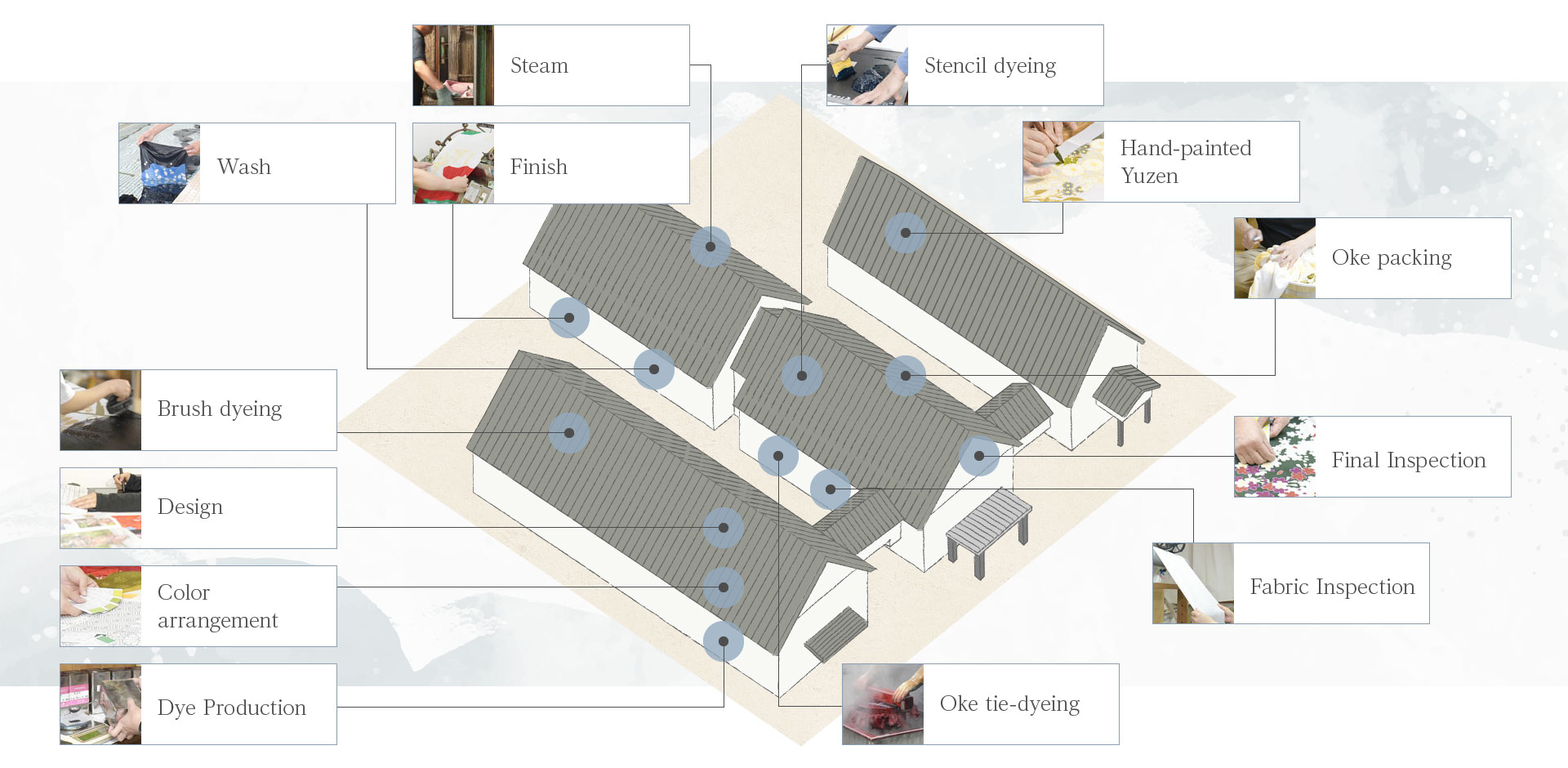
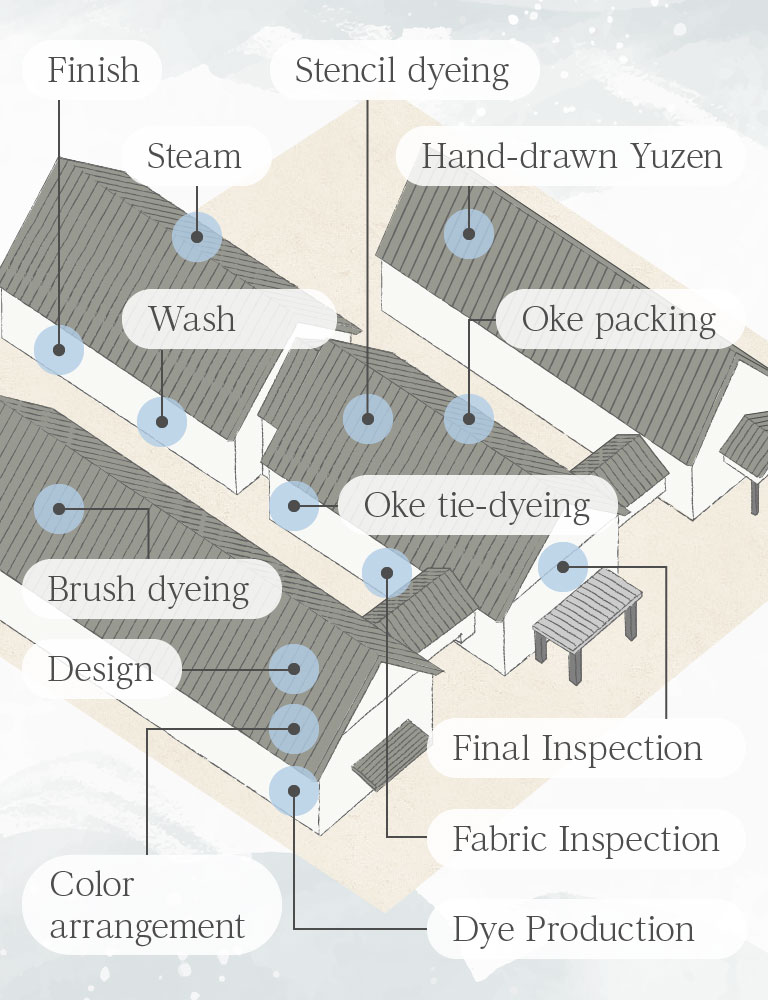
-
Design Process
- Small Design Drawings (Hinagata)
- Full Scale Design Drawings
- Determining the Production Process
- Fabric Selection
- Design
OpenDesign
Always keep inventing new things.
The starting point for product development in Aoyagi is design.
Design is a very important job to devise all about the products
for example market research, design devise, material devise, application technique devise, etc.At Aoyagi, who constantly seeks new things, we value free and flexible ideas and strive for daily development.
scrollColor arrangement
Coloring work is an extremely important work process that determines each color that matches the pattern and determines the ground color.
Color arrangement
We will fully consider the sense of the times according to the product concept and assume that it will be dyed as the final design.
Coloring work is an extremely important work process that determines each color that matches the pattern and determines the ground color.
We choose the dye according to the pattern we want to present.
Because dyes have individuality depending on the type, it is also an important task of color arrangement to combine them well.Depending on the strength and arrangement of the hue used, the most important point is to arrange the colors according to the purpose, such as the stability of appearance, luxury, and atmosphere.
scroll -
- Fabric Inspection
- Temporary Assembly
- Pattern Outlining with Aobana Extract
- Hem Alignment
OpenFabric Inspection
-
Yuzen
- Itome Kaki (Outlining pattern areas with resist paste)
- Stencil dyeing
- Base Color Arrangement
- Dye Production
- Brush dyeing
- Steam and Wash
- Drying
*Some products do not have a Yuzen process.OpenSteam
Steaming time varies depending on the type of cloths, color density, and season
Steam and wash
Hang the some cloths on a wooden frame with a needle called a steaming frame. At this time, pay close attention so that the cloths do not come into contact with each other.
Fill the steaming kiln with steam at about 100 !aC, put a steaming frame, and wait for about 30 to 50 minutes while adjusting the amount of steam.
Steaming time varies depending on the type of cloths, color density, and season, so it may be a repetitive task in some cases.In order to appear the color beautiful, in the case of steaming for the second time or later, the top and bottom of the cloth are swapped and hanged so that the steam hits evenly.
After fixing the dye by steaming, we proceed to the process of washing excess glue and auxiliary agents with water.Put cloths in the water tank while running water, and wash it quickly with a shake or brush so that the glue is softened and peeled off.
If it is not washed with water sufficiently, the texture and color will change to an unintended state.
Therefore, even if the dye or glue seems to have fallen off with the naked eye, we change the water and wash it with water many times to wash out all the excess dye inside the thread and between the fibers.scrollStencil dyeing
The color paste changes slightly depending on the temperature and humidity depending on the season
Stencil dyeing
There are two types of Yuzen: the process of printing with color pastes (*1) layered on top of each other using a pattern(*2),
and the "itome" and "fuse" paste (*3) for coloring with hand-painted Yuzen to prevent dye for the ground color.The number of stencil that make up one pattern of Yuzen, for example furisode, is about 350 to 400 sheets.
The number of colors used for a furisode is about 30 colors, and the period required for processing per pattern is about one week.Because there are many types of pattern and dyes, it is important to use them properly according to the purpose of expression.
The color paste changes slightly depending on the temperature and humidity depending on the season,
and it affects the color feeling after dyeing, so it is necessary to have the skill to dye it without causing unevenness. It is the craftsmanship that counts.(*1) Color paste is a dye that is mixed with paste made from rice or bran.
(*2) Printing with color pastes is the process of mixing dye with glue and rubbing it directly on a cloth. In particular, it refers to a pattern that is rubbed with a dye using a pattern.
(*3) The linear glue that binds the shape of the pattern is called "itome", and "fuse" is a paste made from glutinous rice, bran, etc., and is intended for resist dyeing.
scrollBrush dyeing
Brush dyeing is a method of dyeing the fabric evenly with a special brush or with a blurred representation.
The kimono fabric is about 13m long, so a large space is required.First draw with "aibana" (*1), then pull the cloth with a stretcher and "shinshi" (*2).
By "jiire", it enhances the permeability of the dye to the fabric and improves the color development.
"Jiire" is a pre-dyeing process in which a mixture of douzhi (*3), gliopeltis (*4), and an auxiliary agent is brushed evenly on both the front and back of the cloth.After "jire", we will dye the dried cloth.
At the boundary of dyeing liquids with different colors and concentrations, brush dyeing is performed while spraying water.In order to dye evenly and evenly, the experience of skilled craftsmen and speedy handicrafts are required.
(*1) Aibana is dyes used for drafts of Yuzen dyeing.
It is made from the blue flowers of Asiatic dayflower and is water-soluble, so it disappears after dyeing.(*2) Shinshi is a bamboo stick with a length of about 40 cm with needles implanted at both ends.
Flatten the cloth by sticking "shinshi" needles into the left and right edges of the cloth.
Approximately 80 "shinshi" are used to dye one kimono.(*3) Douzhi is a liquid made by soaking soybeans in water, and then crushing and straining them.
(*4) Gloiopeltis is a liquid made by boiling seaweed called gliopeltis on a simmering fire and straining it.
scrollWash
Even if the dye or glue seems to have fallen off with the naked eye, we change the water and wash it with water many times to wash out all the excess dye inside the thread and between the fibers.
-
Shibori
- Ito Ire (Stitching resisting thread)
- Hitta Shibori Binding / Koboushi Shibori Binding
- Dye Production / Jizome (Base dyeing)
- Drying
- Oke packing
- Oke tie-dyeing
- Unbinding
- Wash, Steam and Finish
OpenDye Production
Oke packing
The fabric endures the power of 500 needles and a straw rope and waits for the finish.
Oke packing
In the "oke tie-dyeing" that symbolizes Aoyagi, "Oke packing" determines the finish of tie-dyeing.
The fabric is tied to the old-fashioned cypress cask,
but if the needle used at this time is weak or the binding method is loose, the dyeing liquid will leak into the gap.
"Oke packing" is an important work that requires delicate manual work and power.In various rough processes, the fabric endures the power of 500 needles and a straw rope and waits for the finish.
The cask, which wears and becomes thinner every day, still protects the cloth.When craftsmen and tools communicate with each other toward the same goal that means product completion,
we cannot help feeling a strong bond and love.scrollOke tie-dyeing
It is only with this process that Aoyagi's original kimono is born.
Oke tie-dyeing
The cloth is dyed beautifully only when the "oke-packing" craftsman and the "oke tie-dyeing" craftsman breathe together.
Soak the kimono packed in "oke" in the dyeing solution at 85-90 degrees for about 20 minutes.
During that time, a technique for quickly dyeing an "oke" weighing 25 kg while moving it up, down, left and right is required.Because boilling water is used, craftsmen wear two pairs of rubber gloves
and put cold water in the gloves to prevent the skin from being directly exposed to boilling water.
Craftsmen wear waterproof aprons and boots to prevent boiling water.It is a rough work that is disproportionate to beautiful kimono, but it is only with this process that Aoyagi's original kimono is born.
When you open the lid of the dyed "oke", the beauty of the white inside the resist dye gives off a exceptional shine.scrollFinish
-
Yuzen
- Ji Ire (Brushing a starch solution on the fabric)
- Dye Production
- Hand-drawn Yuzen
- Steam, Wash and Dry
*Some products do not have a Yuzen process.OpenHand-drawn Yuzen
Aoyagi's strongest field is the combined use of tie-dyeing and Yuzen dyeing.
Hand-drawn Yuzen
Craftsmen can add colors as they wish by using a brush that fits in their hands.
Aoyagi's strongest field is the combined use of tie-dyeing and Yuzen dyeing,
in which hand-painting is added to the fabric that has been tie-dyed with resist dyeing paste.
Hand-drawn Yuzen is the final process of creating and expressing bold and delicate colors by mixing dyes.The compatibility between the brush and the color, which brush to use when drawing with a dark dye, is also an important factor.
Colors, brushes, and fabrics react very delicately to temperature, humidity, and wind.Working while coordinating with temperature, humidity, and wind and having a deep relationship,
sometimes goes beyond the idea of thinking on the desk and creates a more beautiful and more natural pattern.The number of colors is infinite.
The colors in each person's mind are different, which is also fun.scroll -
Inspection
OpenInspection
-
Decoration
- Haku (Gold and silver foils)
- Kindei (Gold paint)
- Embroidery
OpenHaku (Gold and silver foils)
It's a joy to work with a process that can change the mood and feel of the design.
-
Final Stages
- Assembly
- Final Inspection
- Delivery
OpenFinal Inspection
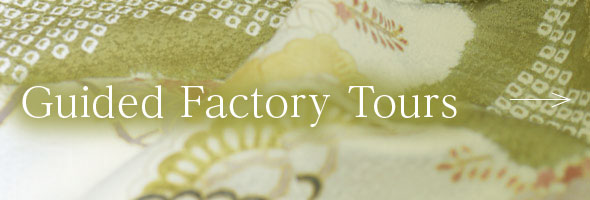
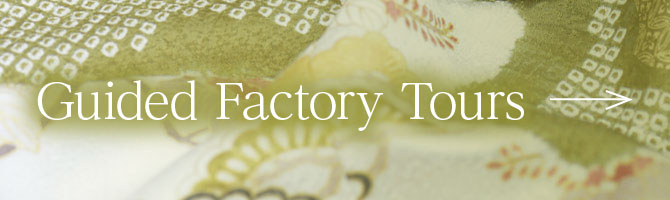